American Cladding Technologies Becomes a Division of Joining Technologies
EAST GRANBY, Conn., February 6, 2023 – American Cladding Technologies, a leading provider of laser metal deposition services for the past decade, has announced it will begin operating as a division of Joining Technologies. Both companies are owned by Joining Industries, Inc.
Greg Miller, President of Joining Technologies, says the decision was made in order to “streamline our operations and deliver better overall service as one company operating under a single management structure.”
This shift in operations is expected to be nearly seamless, as both companies were already sharing certain resources, including sales, marketing and quality engineering.
American Cladding Technologies (ACT) will move its equipment and staff to the Joining Industries Headquarters building at 17 Connecticut South Drive, just a quarter of a mile away from its current location at 15a International Drive. ACT will take over the space currently occupied by JT Automation, another Joining Industries company, which will move to a newly acquired property in Windsor in April 2023.
Although ACT will go forward as a division of Joining Technologies rather than a separate company, they will continue use of the American Cladding Technologies brand and website www.americancladding.com. Forthcoming web updates will establish a clearer connection to Joining Technologies.
About Joining Technologies
Joining Technologies is a leading provider of precision welding, machining, and build-to-print services. For over 30 years, the company has developed solutions for organizations nationwide with focuses in aerospace, automotive, defense, energy, firearms, medical device and semiconductor manufacturing. Located in East Granby, Connecticut, the Joining Technologies facility is equipped with cutting edge laser welding, electron beam welding, resistance welding, wire EDM, laser cutting, and laser cladding stations.
As a member of the Joining Industries family, the company’s mission is to “create a platform where meaningful business happens, and to leverage it to improve the lives of everyone we can possibly touch,: our employees, our customers, our suppliers, our community. This is our guiding light, our True North.”
To learn more visit joiningtech.com and follow us on LinkedIn for the latest company news.
The Heat Affected Zone
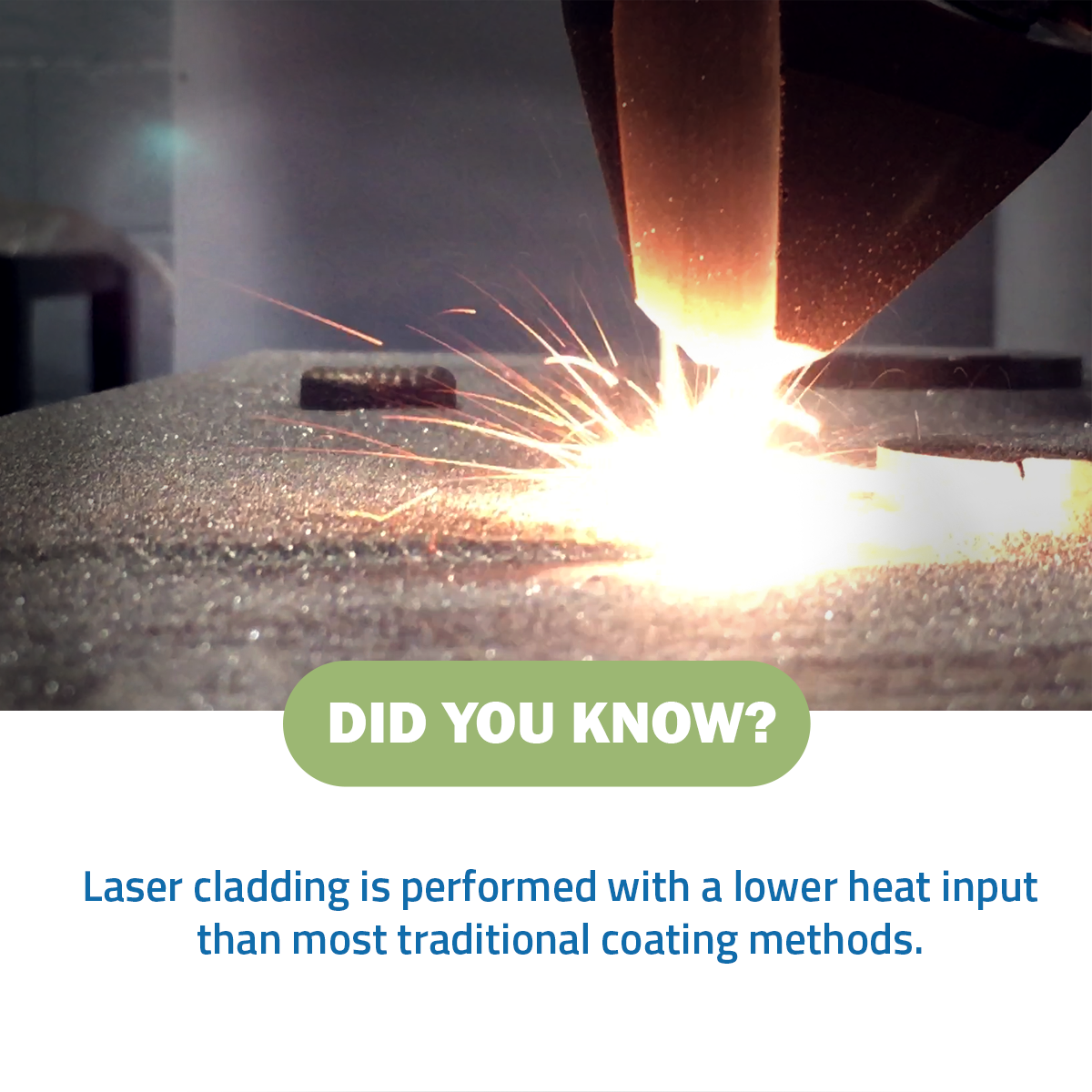
Our customers often ask about the impact of the Heat Affected Zone (HAZ) on their components, and for good reason. The HAZ can weaken the component and potentially lead to failure. But rather than crossing laser cladding off your list of preferred processes, there are ways to mitigate the HAZ.
What is the Heat Affected Zone (HAZ)?
The heat affected zone is a region just below the weld/base material interface. It’s an area of base material that was not melted, but the localized temperature was raised. This can cause the microstructure and material properties of the base material to change.
The depth of the HAZ can vary depending on process variables.
These variables include:
- Base metal type
- Thermal contact time
- Geometry of the component
- The amount of energy applied
How will the heat affected zone impact my components?
If the original material properties are critical to the design or performance criteria of the component, designers must consider the HAZ. This microstructure change can result in reduced strength, increased brittleness or lower corrosion resistance. The HAZ can definitely be an issue for more demanding applications, especially for the aerospace industry, industrial gas turbines, and for downhole applications in the oil & gas industries. However, designers will often take the HAZ into account when designing their components.
What is the smallest heat affected zone that you can achieve?
Unfortunately, the answer is not always straightforward. We have used the laser metal deposition (LMD) technique for our aerospace clients that resulted in a HAZ so small we were unable to measure it. However, the process techniques used to accomplish this may not always be economical for some of our other customers. A more general value for HAZ in most applications is around 0.003” – 0.008”.
Another solution for dealing with the HAZ is to perform a post-weld heat treatment (PWHT). However, depending on the components, this can sometimes be too costly or impractical. PWHT is not an ideal solution if there is concern about initiating distortion into other regions of the part.
Here’s where laser cladding offers an advantage
The laser cladding process allows us to control the heat input of the laser very precisely. Laser cladding produces a much smaller heat affected zone compared to PTA, GTAW or TIG welding, which have higher heat inputs. Components treated with laser cladding are more manufacturable, and may not require post-weld heat treatments.
This blog post just scratches the surface of this topic, so talk to your laser cladding specialist to discuss the specifics of the HAZ for your application and learn how you can beat the heat.
The Chrome Plating Alternative You've Never Heard Of: Laser Cladding
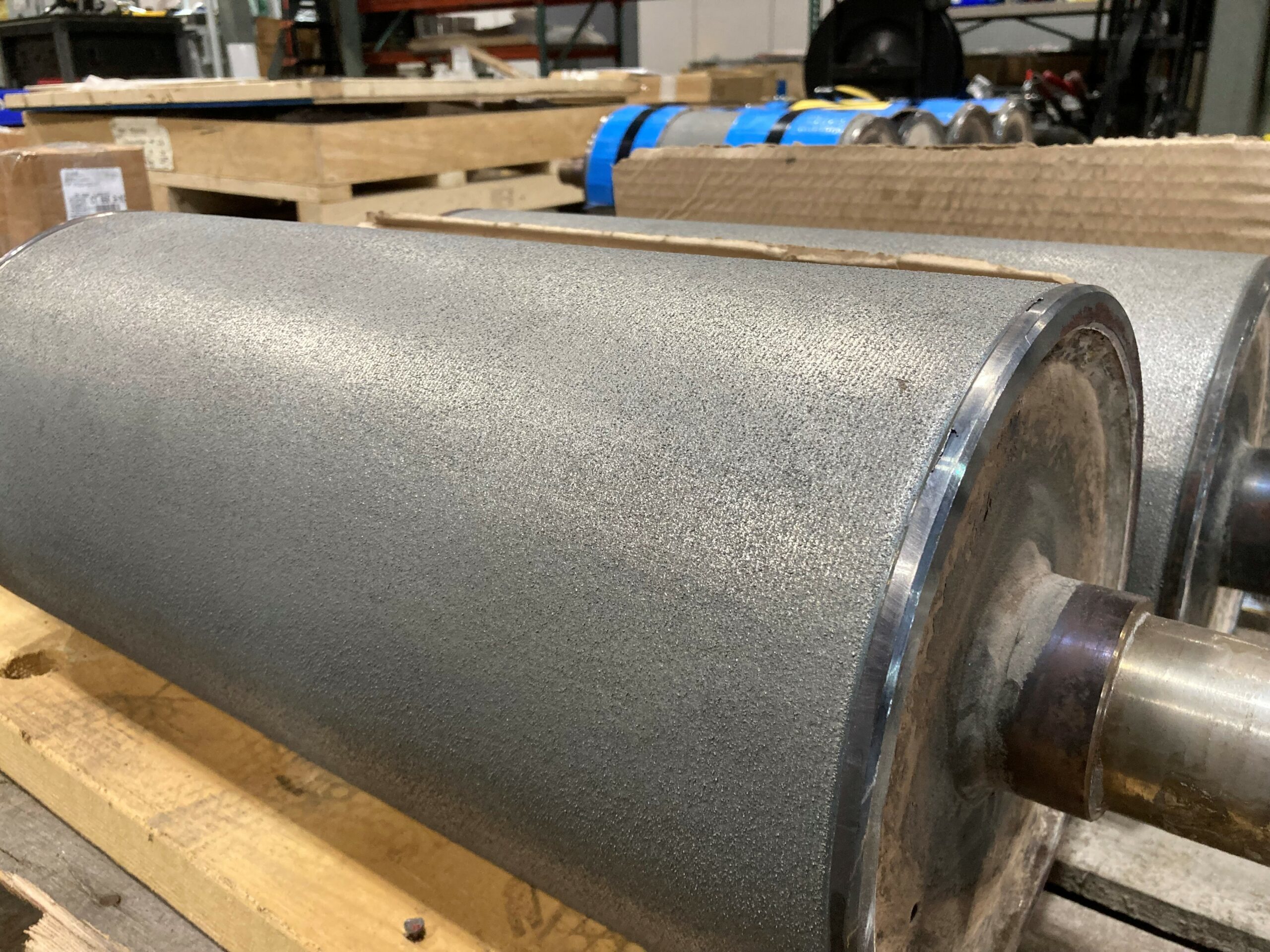
Why do steel mills need a chrome plating alternative for steel mill rolls?
To understand why steel mill operators may want to choose a chrome plating alternative, we need to think of the working conditions inside of a steel mill.
If you’ve ever been inside an operating steel mill, you quickly learned two things:
1) It’s unimaginably hot in there.
2) The equipment takes a severe beating.
Perhaps the hardest working components in the facility are the steel rollers. Steel rollers form the steel, shape it, and move it through the plant for processing. When shipped from the factory, the rollers are typically plated with chrome. Chrome is durable, resists corrosion and has good impact resistance. But in reality, due to their extremely demanding working conditions, most chrome plated steel mill rolls don’t last longer than 6 months. Roll surfaces get damaged, worn down, and become uneven. The metal becomes stressed and fatigued.
Problems caused by roll fatigue
1) Reduced steel mill performance and process efficiency
2) Increased downtime
Downtime can lead to loss of resources, profitability and, in some cases, missed delivery deadlines.
3) Diminished product quality and consistency
Damaged rollers can lead to product defects.
4) Replacement rolls are expensive
When repairs aren’t feasible, new rollers are needed in short cycles, but with long lead times.
The good news is that there is a chrome plating alternative that yields a much more durable roller surface: laser cladding with tungsten carbide.
Stronger coatings applied with laser cladding
Unlike many other surface hardening methods, laser cladding creates a true metallurgical bond to the base material. Our favorite metal powder to use for coating steel mill rolls is a Tungsten carbide blend. Tungsten carbide can provide a coating that is approximately double the stiffness of steel, and with twice the density. When combining the unique traits of the laser cladding process with the impressive properties of tungsten carbide, several major benefits are realized:
- Increased Thermal Resistance
Rolls clad with Tungsten carbide can withstand over 5,000°F. Chrome plated rolls can withstand 3,000°F. - Significantly Improved Longevity
Due to the higher stability of tungsten carbide, the rollers can withstand more stress and last four times longer on average. - Decreased Downtime
The increased life cycle means less downtime, and all of the headaches that are associated with it.
At a time when every dollar counts, increasing efficiency is more important than ever. Steel mills that have recognized the benefits of laser cladded rollers over chrome coated ones enjoy reduced costs and downtime, increased profitability, and quality, consistent output.
If you are wondering if your bottom line can benefit from laser cladding, please reach out to one of our application engineers. They’d be happy to review your needs and propose an innovative solution.
Thermal Spray Alternative: Laser Cladding
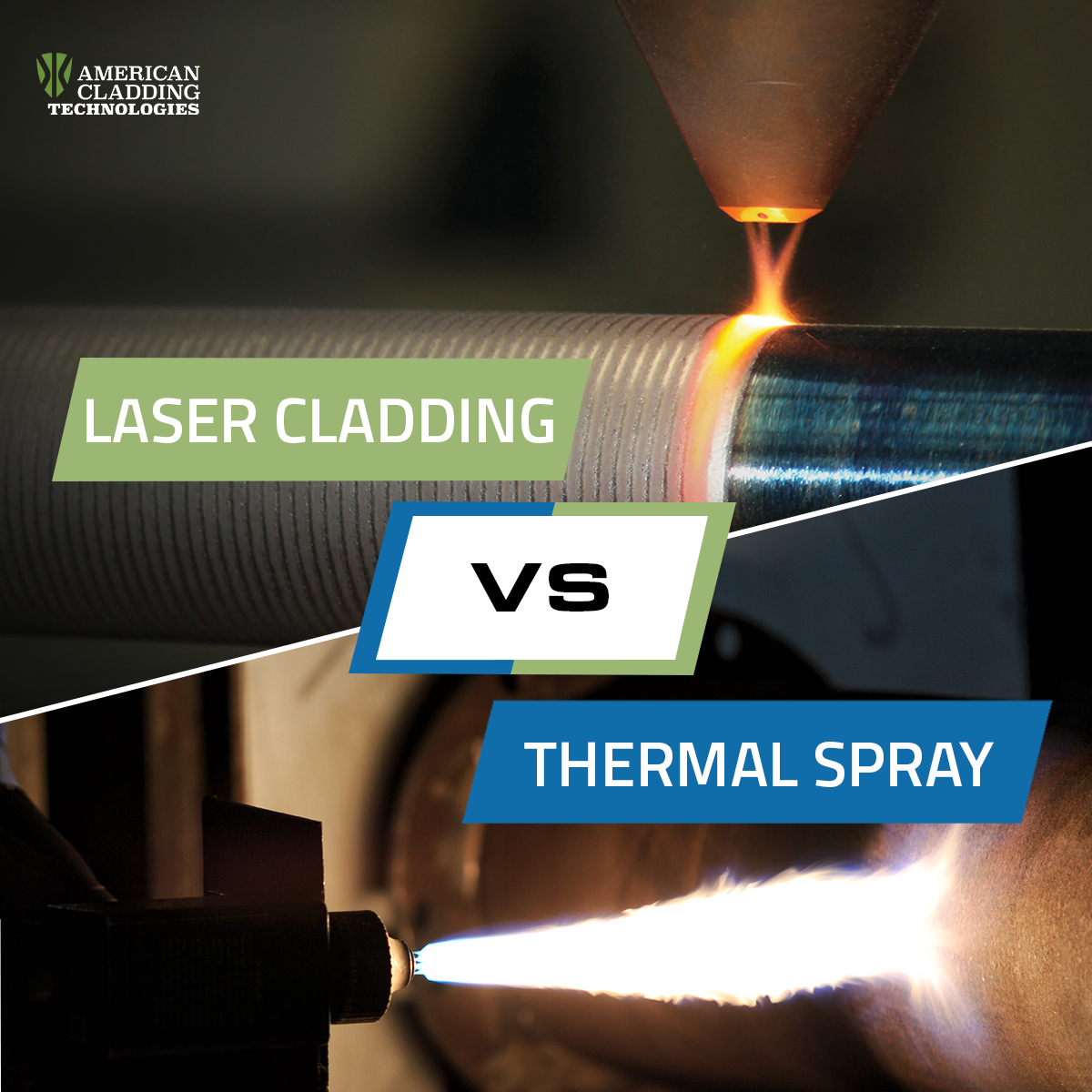
Exploring Laser Cladding as a Thermal Spray Alternative
Whether you’re looking to restore heavy duty industrial components, or extend their lifetime before installation, this guide will help you evaluate laser cladding as a thermal spray alternative.
Laser Cladding & Thermal Spray Defined
Let’s start with a quick review of how each method works.
Laser cladding is an additive process. A laser heats the metal and deposits layer by layer onto a metallic substrate. This process manufactures, strengthens and restores heavy duty industrial components such as pump shafts and turbine blades.
Thermal spray is also used to restore surfaces, although it works a bit differently. One thermal spray process, HVOF (high velocity oxygen fuel coating) mixes fuel and oxygen, which travel into a combustion chamber and ignite. The resulting hot gas flows through a nozzle at extremely high speeds. Powder is added to the mix and is used to coat the workpiece.
Other variations of thermal spray include plasma spray, wire arc spray, flame spray, and high velocity air fuel spray (HVAF).
Both laser cladding and thermal spray restore and enhance hardworking components. Each process applies a coating designed to withstand harsh conditions. Corrosion resistance and wear resistance are two of the top issues mitigated by adding a coating.
The Key Differences Between Laser Cladding and Thermal Spray
There are a few key differences between the two processes:
Laser cladding forms a true metallurgical bond
One form of laser cladding called “Laser Metal Deposition” (LMD), uses inert gas to deposit alloyed metal powder into a laser beam creating a weld pool onto the substrate. The weld interface between the substrate and the filler material is classified as a metallurgical bond, and has a higher bond strength when compared to thermal spray applications. Coatings applied with laser cladding have minimal dilution and the finished product contains little to no porosity.
Thermal spray processes creates a mechanical bond where the coating adheres to the substrate of the component by means of a friction or interlocking bond between the base and additive material. It is not a metallurgical bond. This can result in a porous coating, which is a big reason to use laser cladding as a thermal spray alternative.
Laser cladding can deposit thicker coatings than thermal spray
Laser cladding can produce coatings up to ~3.5 inches (76mm) thick, while thermal spray can go up to 1mm or so (or less) before issues, such as spallation, start occurring. Thickness is also easier to control with laser cladding.
It’s also worth noting that thick coatings aren’t always necessary. Full material properties can be achieved by applying thinner coatings, saving money on powder costs.
Laser cladding can coat internal diameters
Using a laser allows us to coat the internal diameters of tubes, pipes, and cylindrical components using a process called I.D. Cladding. This type of coating is tougher to achieve with thermal spray processes, though not impossible.
Thermal spray is portable
Laser cladding happens in a stationary facility. Thermal spray is portable. This is helpful for applications where field service is preferred, such as machinery used in the construction industry. Let’s take bucket loaders for example. They work hard, digging, scooping and moving sand and other material around all day long. The resulting friction causes the teeth to wear down. It’s quicker and more efficient to service these in the field with a portable thermal spray operation, rather than in a plant. However, for new equipment, OEMs may prefer laser cladding due to the increased durability and longevity it provides.
Application Examples
Boiler tubes
Laser cladding performs extremely well with applications that require a lot of thermal cycling, such as waste to energy boilers. Here, the tubes heat up to 1600/1800°F, then cool, and then heat up again. When the coating expands at a different rate than the tube, the shear force at the bond interface can lead to premature failing or spalling. This can cause pieces to chip or break off. The shear force can be quite severe, causing costly downtime if the superheater tubes aren’t properly treated.
Working steel mill rolls
In steel mills, hot molten metal pours from furnaces onto rollers which shape products ranging from flat sheet metal to I-beams. As you can imagine, these rollers wear out quickly, thanks to the temperature differential. Rollers coated using HVOF are likely to chip and get damaged. These impaired areas allow water to get in, causing the roller to degrade very quickly. With a metallurgical bond, the metal will not chip or flake, and will be more resistant to abrasion.
Should I Use Laser Cladding as a Thermal Spray Alternative?
It depends! Here are a few cases where we recommend laser cladding:
- If your component has high impact requirements.
- You’d like to achieve a strong metallurgical bond created with relatively low heat input.
- You dream of a one-step process with minimal post-processing required.
- If the component can be transported and coated in a facility like ours.
- To enhance the interior diameter of your component.
What's the Difference Between Laser Metal Deposition and 3D Printing?
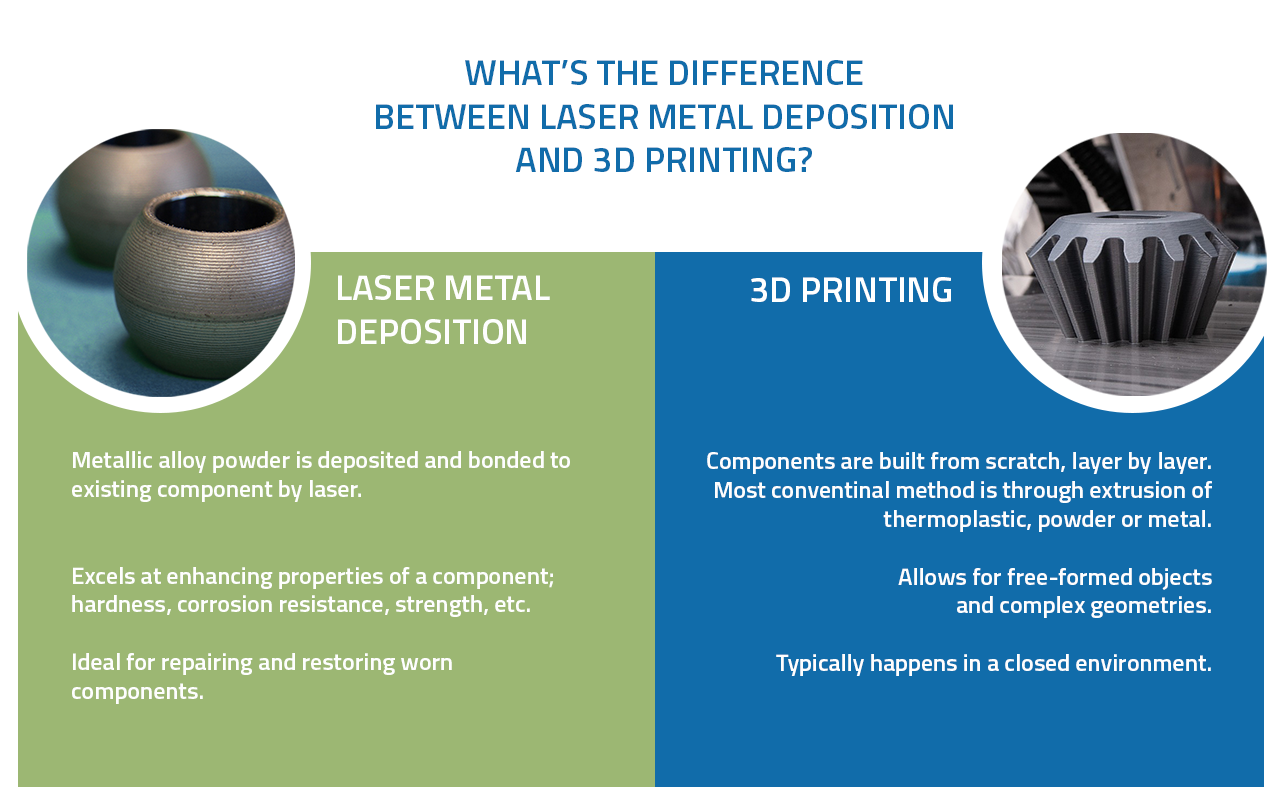
We’re often asked to compare laser metal deposition and 3D printing. Both processes can be labeled “additive manufacturing,” but do the similarities end there? In this article, we’ll explore how each process works, and the different applications for each technology.
What is Laser Metal Deposition?
Laser metal deposition (LMD) is an additive manufacturing process in which metal is heated by laser and deposited onto a metallic substrate, layer by layer. It is also known as laser cladding, although technically, laser cladding is a type of laser metal deposition. Laser metal deposition is used to manufacture, strengthen, and restore parts such as turbine blades, pump shafts, and pressure vessels, just to name a few.
Let’s take a closer look at how the process works. It starts with the laser which heats the surface of the workpiece. A nozzle then feeds powdered metal in the melting pool, fusing it to create a metallurgical bond with the substrate. The process is repeated, building one layer at a time. The result? Parts that are strong, with incredible wear resistance due to increased hardness. Popular powders (or wire) used in laser metal deposition include Inconel, cobalt, Hastelloy, tool steels and many other metals including super alloys.
The Process is the Finish!
Laser metal deposition is a fantastic choice for protecting components that are hard-working or difficult to replace. The finish created by laser metal deposition is extremely durable, and ideal for applications that are subject to intense abrasion, such as downhole drilling or mining operations. The treated surfaces also boast strong corrosion and erosion resistance, which is required for heavy duty critical components found in aerospace, power generation, valve, and similar demanding applications.
Is Laser Metal Deposition the same as 3D Printing?
While the processes appear similar, laser metal deposition and 3D printing both excel at completely different things. For our example, we’ll examine the more conventional approach to 3D printing, which involves the extrusion of thermoplastic material, powder, or metal.
3D printing builds components in layers, just like laser metal deposition. However, 3D printing is better suited for creating free formed objects, as well as those with more complex geometries. Such objects may not be ideal candidates for laser metal deposition.
Additionally, 3D printing typically happens in a closed environment, so dimensional capabilities are restricted by the size of the system’s enclosure. At American Cladding Technologies, laser metal deposition is limited only by the size of our facility. The components we service can be as small as a half dollar, or as large as 40 feet long, 6 feet in diameter and 6 tons in weight.
Laser Metal Deposition: The Choice for Durability, Longevity and Strength
Whether you need to process new parts, restore old ones, or bring obsolete components back to life, laser metal deposition will often outperform other methods. For instance, when used on boiler tubes for chemical processing or waste energy, those coated with Inconel 625 will last 6 times longer that than those without treatment. Laser metal deposition is a fast and efficient process that delivers durability and longevity to many hard-working, mission critical components in the most demanding applications.
Hardfacing Working Steel Rolls
Hardfacing working steel rolls is a worthy investment in component lifetime, paying for itself by reducing the frequency of downtime resulting from worn down equipment.
Whether you are talking about calendaring rolls, spreading rolls, leveling rolls, drawing rolls or high temp rolls, working steel rolls are ubiquitous in many industries. Whether it be paper, textiles, or steel, many products we use every day were manufactured using working steel rolls of some type. These manufacturers all use working steel rolls to shape, form, strengthen and convey materials through the manufacturing process.
Over time, the surface of the rolls will degrade, leading to costly line down time or poor-quality manufactured materials. For this reason, steel rolls are expensive consumables in the manufacturing process. We see a variety of rolls issues, including changes in roll diameter and surface quality.
In many cases the lowest hanging fruit for reducing production costs associated with line downtime is the fast and efficient refurbishment of the steel rolls. There are three common methods used to repair working rolls which are plasma spray, HVOF and laser cladding.
Plasma Spraying – a process in which the material to be deposited (typically a powder, liquid, or wire) is introduced into a plasma jet emanating from a plasma torch. The material is melted to the order of 10,000 K and propelled towards a substrate. The molten material then rapidly solidifies leaving a deposit adhering to the substrate.
High Velocity Oxygen Fuel Spraying (HVOF) – a mixture of gaseous or liquid fuel and oxygen is fed into a combustion chamber where they are ignited and combusted continuously. The hot gases created by the process are at a pressure close to 1 MPa and emanated through a converging-diverging nozzle and travels through a straight section. The velocity at which the gasses exit the barrel can exceed the speed of sound. A powder feed stock is injected into the gas stream, accelerating the powder up to 800 m/s. The stream of hot gas and powder is directed towards a substrate where the powder then melts and is deposited onto the substrate. The result is a low porosity coating.
Laser Cladding (Laser Metal Deposition) – a method by which an engineered metal powder or wire feedstock is melted and consolidated using a laser to coat a substrate or fabricate a near-net shape part. The interaction of the engineered powder, laser and substrate produces a melt pool. As the laser moves across the substrate, it leaves a track of solid metal. This creates a metallurgical bond versus an applied coating.
Laser cladding could be the key to dramatically reducing downtime in these industries. By using lasers and engineered metal powders to resurface (also known as hard facing or hard surfacing) the diameter of the steel rolls, we can restore the diameters of the steel rolls to a like new or even better than new condition. Typically, the surface of a laser clad roll is harder and more resistant to corrosion and wear than a new unclad roll. This is due to the metallurgical bond that is created vs. a traditional coating. A metallurgical bond is the result of chemical bonding that occurs between a substrate and the engineered powder or wire feedstock. Laser cladding can obtain the best balance between the two materials being bonded together. This bond can be adjusted to enhance properties such as:
- Hardness
- Toughness
- Strength
- Performance in extreme temperatures
- Fatigue
- Corrosion resistance
- Weight
If your production facility uses working steel rolls and is looking to dramatically increase the useful life of the rolls (up to 10x), in turn reducing downtime, then you should be looking into hardfacing with laser cladding technology. If you are ever in doubt of which process to use, just ask a trusted metallurgist whether a laser clad metallurgical bond is superior to a sprayed or applied coating. You will likely find that laser cladding will be the top choice to outperform the others by providing stronger, longer lasting equipment.
Working with Reade Advanced Materials: Meet the Laser Cladding “It Guys”
Thank you to Reade Advance Materials for their kind article about our team here at American Cladding Technologies, what we do, and our experience working together.
“Self-described as the American Cladiators, the team at American Cladding Technologies (ACT) are the “it guys” for getting tough jobs done. ACT specializes in laser cladding technologies and additive manufacturing to strengthen, restore and improve surfaces of metal parts. These parts such as valve balls, hard facing screws, nozzles, plates or drill bits are used in an array of industries ranging from nuclear power generation, aerospace, public infrastructure, and oil and gas exploration. ACT most typically uses tungsten carbide, stainless steel, titanium carbide, Inconel 625 and aluminum silicon magnesium alloys in their deposition process.
So what exactly is laser cladding? The process of laser cladding works by adding metal alloy powder layer upon layer as a bond onto a base material or substrate. “Powdered alloy is delivered through a powder feed system (vibratory or rotary disk) using a carrier gas such as argon or helium. The powder is delivered through a non-static plastic tube to the nozzle head. The powder is delivered to the melt pool either coaxial or through discrete streams depending on the nozzle type used. Off-axis powder delivery is commonly used as well” explains Chris Proulx, ACT’s Vice President of Sales and Marketing.
The process protects the integrity of the original substrate and is a very low heat process with a low heat affect zone, resulting in little to no distortion. Their services are designed to improve the metal part by adding protective layers for erosion, corrosion or further wear. ACT is also capable of repairing parts that are damaged by rust, dents, dings or holes by machining the piece to clean and prep for proper cladding. Their technology can clad a piece up to 40’ in length, 6’ in diameter, and up to 6 tons in weight. ACT’s laser cladding process has been known to extend the life of their customer’s parts well beyond the initial life expectancy.
“We take a lot of pride in our R&D” says Proulx. Their new 20,000 ft2 facility in East Granby, CT can annually process up to 32 tons of powder deposition. Though many of their projects are focused on repair, ACT welcomes OEM projects especially with the recent acquisition of their Trumpf TruPrint 3000 metal 3D printer, which will enable them to design and print parts that were not possible with their earlier machining capabilities.
They are known as the “go to guys” when it comes to laser cladding in the world of high strength wear protection. When companies struggle to coat in house or fix the wear issue of their parts self-sufficiently, they turn to ACT. “We give another layer of options to our customers”, says Jeff Whittaker ACT’s President about their product and surface hardening solutions.
In the world of additive manufacturing, aluminum powders are vital. Their desirable characteristics of fine microstructures, high heat conductivity and low weight make for ideal performance characteristics when compared to other alloys. Recently, ACT purchased aluminum magnesium silicon powder from READE for a space exploration project that required powders best suited for highly corrosive environments where weight is a limiting factor. Their customer needed a free form aluminum tube and their bespoke manufacturing capabilities were called upon. “READE was great to work with, very responsive and helpful in identifying different aluminum alloys” says Whittaker.
Working closely with custom manufacturers is one of the many highlights of managing accounts at READE. The spirit of a can-do attitude runs deep at ACT. Their custom process is designed to meet the needs of their customers while adding the desired performance characteristics (wear protection) to the parts they are working on (tasked with improving). Likewise, READE, offers customized powder solutions to customers while focusing on quality and meeting customer demands in today’s fast paced industrial marketplace.
READE looks forward to a mutually rewarding relationship with ACT as they embrace their new 3D printing capabilities and expand their products and services to an ever-changing customer base.”
Full Article Here:
Bespoke Laser Cladding Nozzles Made Possible w/ Powder Bed Fusion
We were recently featured in an article by “Additive Manufacturing” depicting our use of powder bed fusion (PBF) metal 3D printing to expand our portfolio of manufacturing services. In the PBF process, loose powder is contained in a build envelope and melted point by point with a laser. Currently, this capability is being used to make production parts for our customers, but is also serving another, internal purpose: building custom nozzles to improve the efficiency, performance, and cost of its laser cladding operations. Click the link below to learn more:
Corrosion Solutions for Power | Laser Cladding
The Need for Corrosion Solutions
Harsh environments are a fact of life in the power generation industry. Equipment is subjected to all kinds of abuse, from high temperatures and high pressure to fuel that is highly corrosive and erosive.
Laser cladding, also known as laser metal deposition (LMD), can solve many of these challenges by providing a highly corrosion-and erosion-resistant coating that extends the life of expensive components.
Compared to traditional additive processes, LMD provides corrosion-resistant coatings with:
- a strong metallurgical bond with higher material hardness
- less stress due to lower heat input
- lower powder costs due to thinner coatings
Here are just a few examples of how this corrosion solution can extend equipment life and prevent unplanned downtime in the power generation industry:
Superheater tubes: Laser cladding can significantly reduce corrosion in boiler tubes. Boilers at waste to energy facilities are subjected to temperatures of 1,600° – 2,000° F and pressures from 850 – 1200 psig. Typical superheater lifespan with Inconel 625 overlays is 16-24 months, after which the entire primary and secondary superheater is usually replaced at significant cost. By cladding a highly corrosive and erosive resistant coating onto the superheater tubes and platens, we have increased their lifespan from 16-24 months to 6 years.
Soot blowers: Soot blower lances are exposed to the same harsh environments as superheater tubes, resulting in downtime and high maintenance costs. Laser cladding the lances have extended their lifespan up to 6 times, reduced replacement costs, and significantly reduced maintenance time.
Valve applications: Valve balls and seats, and valve housing and casings are also exposed to extreme conditions in power generation plants, prompting the need for corrosion solutions.
LMD can mitigate wear and/or corrosion using a typical coating thickness of 0.025” to 0.050” and can achieve a coating hardness up to 70 HRC within 0.005”-0.008” of the base material.
Pump applications: In a centrifugal pump, wear of the impeller or other pump components can be worsened by suspended solids. In many cases, a wear-resistant laser clad coating can be applied to extend the component lifespan, or original material can be applied to the wear location to allow for component restoration.
In a twin rotary screw pump, the top flight of a screw is exposed to metal-to-metal rubbing contact with the casing or adjacent shaft screw, causing wear. To prevent wear, a laser hardfacing coating forms a metallurgical bond rather than a mechanical bond commonly found in thermal spray processes or spray and fuse applications. LMD also prevents wear to pump shafts and shaft components.
Many other components in power generation plants can benefit from using laser cladding as a corrosion solution. If you have questions about equipment not mentioned here, please visit our contact page to request more info.
Hardfacing Internal Diameters with The Help of 3D Printing
American Cladding Technologies (ACT) has made significant advances in hardfacing internal diameters with the help of their TRUMPF TruPrint3000 3D metal printer. Until now, ACT has had to rely on the nozzle designs of the OEM’s. President of American Cladding Technologies, Jeff Whittaker states, “We are now able to design and 3D print our own laser cladding nozzles with features that simply weren’t possible with conventional machining.”
This new design allows for:
- Better shielding gas coverage (lower oxygen in the weld pool means improved metallurgy)
- Increased powder efficiency (reduces cost to the customer)
- Stabilized laser spot size and spot geometry
- Improved cooling in high heat applications from tiny cooling channels throughout the nozzle
With their new nozzles ACT has successfully deposited 65% Tungsten Carbide (by weight) at a thickness of 0.070” (1.78mm) – crack free (see Figure 1). These advances are ideal for adding service life to oil and gas equipment, pumps, sleeves and extruder components.